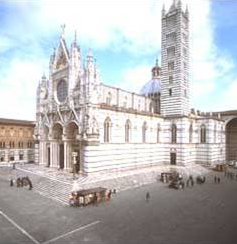
During the recovery operations on existing buildings, strengthening works often involves the insertion of metal elements into the masonry or wooden structures: the stitching up of small damage, the joining of the supporting metal elements to existing structures, the joining of binders to perimeter walls, the strengthening of lofts or wooden roofing.
Anchoring, link-ups and stitching can become one with the masonry or wood through mortar or resin injections. Depending on the application and on the type of material involved, injected anchoring could require different types of intervention: resin injections are fairly simple when the anchoring lengths are less than 1.00-1.50 meters while, for longer lengths, you need to use cement mortar injections compatible with the original materials.
Resin thixotropic used normally for anchoring guarantees against excessive spreading in the wall gaps, but the short curing time complicates the deep extrusion stage. On the other hand, the use of epoxy resins though characterized by long hardening and handling times offers, in this case, the best results and permits going deeper for better anchorage.
On the contrary, mortar which is more fluid, is easily injected, but can get lost in the wall gaps, spaces and damage thus hindering the filling up of the hole and giving no anchoring guarantee. A solution to these problems can be found by applying new, innovative technology recently introduced in Italy by Bossong SpA, which foresees a kind of fabric sleeve wrapped round the metal bar and guarantees total control over injection and adherence with the substrate along the whole length.
Resin joining permits the creation of small holes in the sub-layer, of a diameter just a few millimetres bigger than those of the metal element, thus not invasive and even reversible by drilling a larger diameter; on the contrary, mortar applications need larger diameters requiring the use of special coring with diamond cores that only rotate.
If on the one hand there are technical, theoretical reasons for deciding when the anchoring should be done with resin or cement mortar, that limit is not always so well defined during applications as many other factors, such as compatibility with original materials, are involved and these can limit the choice of materials or just simply cause executive feasibility problems.
This report includes two practical pure epoxy resin application cases during recovery intervention on historical buildings: consolidation of the roof coverage in the Church of Santa Maria Maggiore in Bergamo and pull-out tests on walls on site in Santa Maria della Scala in Siena, Tuscany.
The Church of Santa Maria Maggiore is situated in the heart of the Città Alta old town in Bergamo, in Piazza del Duomo. Built in 1100 as a vow to the Madonna, the Church has kept, externally, the original Greek cross Romanic structure while inside, modified in the 1500s and 1600s it has been enriched with art contributions going back over eight centuries.
The Church roofing is extraordinary and is much admired for the size and power of the plant: two thousand square meters of massive slate tiles from the slate quarries in the Brembana Valley. It weighs hundreds of tons and is supported by a mass of strong English oak and chestnut beams, no longer original but probably late Middle Ages and not replaced after that.
The roof has validly withstood atmospheric agents for hundreds of years and has obviously suffered despite maintenance intervention carried out regularly over the years, but now difficult to manage as, in our days, intervention of that kind becomes more and more complex and costly for safety reasons.
As much as possible, the old roof’s slating has been recovered and reused together with new slating and placed directly on the large beam frame and flooring using special nails.
The wooden structures, almost all recovered, were restored and this confirmed how exceptionally strong they are.
As far as the static part is concerned, the most difficult operation involved two of the large stone wall arches, formed by large, perfectly square elements, supporting the main Nave roof’s wooden structure.
According to the original building plan, the roof’s main wooden frame is made up of beams fitting into the arch walls, causing strong, concentrated loads due to the weight of the slate roofing.
The intervention needed to repair the structure was carried out by inserting, where the beams fitted into the walls, metal supporting structures that could transfer the load to the arches’ extrados surface thus distributing loads better.
We also had to foresee insertion of inclined stitch bars to reinforce the damaged walls.
Based on the intervention project and on specific provisions, the joining of the metal elements, anchoring bars for the metal brackets and stitch bars required Bossong BCR-400 EPOX pure epoxy resin to guarantee the following results: no shrinkage and long curing times allowing medium-long term handling of the resin, necessary in this specific case where the resin injection was carried out deep down (bars longer than 1.00 m) using special extensions.
To carry out the operations needed to consolidate the arches, we used the most advanced techniques and highly specialized labor, considering the special conditions and the precious context being worked in. Under the roofing, the Church holds its precious treasure and not just in the main Nave, richly decorated with stuccoes and decorations, but also in its vast garret areas which contain some wooden Leonardo wheels that laborers of years gone by used to hoist up the material needed to build and repair the roofing.
The intervention went through the following stages:
Stage1: Drilling
The first operation was the masonry drilling to insert the stitching and strengthening bars. To avoid vibration and drumming effects on walls, diamond probe coring elements were used, which just rotated. As work was on the structures above the central Nave vaults, dry drilling had to be used to avoid any damage to the precious decorated surfaces and so as not to create humidity in the walls. The special conditions due to the extrados surface slope on which the coring machine was placed, together with the limited thickness of arch walls, just 50 cm, made drilling operations even more difficult. Drilling lengths go from 1.00m to 1.50m at variable inclinations, as shown in the intervention diagram, while the hole diameter is 30mm.
Stage 2: Hole cleaning
To guarantee the effectiveness of chemical anchorage, the holes must be cleaned thoroughly with special equipment: in this specific case aspirators with extensions able to suck up waste and dust were used.
Stage 3: The epoxy resin injection
To inject the Bossong BCR-400 EPOX epoxy resin, the extrusion had to be carried out with the special Bossong BOSS-400 E-PN pneumatic pump and relative extensions to guarantee filling 2/3 of the hole volume starting from the bottom.
Stage 4: Bar insertion
After resin extrusion, the bars were inserted: threaded M24 stainless steel bars varying in length from 1.00m to 1.50m
The site: Restoration to the lantern and roofing of the Church of Santa Maria Maggiore
Building company: Ing. G. Pandini Restauring Building Company – Bergamo Italy
Drilling: Tecnic Tecnologie srl - Monticello D’Alba (Cn) Italy
Supply and technology consultancy: Bossong SpA fixing systems - Grassobbio (Bg) Italy
The Santa Maria della Scala complex in Siena, Tuscany, one of the oldest European hospitals, has no longer been a hospital for some years and is going through an important recovery operation to be used for museum and cultural purposes.
These works have permitted recovery of some important architectural elements such as columns, arches and coffered ceilings and reconstruction of those fascinating, ample spaces that, though the centuries, surrounded the original complex cores but had been lost because of transformation carried out over recent years.
To permit consolidation of the existing pillar foundation structure, a provisional structure was designed to bear the pillar load and transmit it to other structure supporting elements thus making it possible to operate on the foundations.
To join the metal structure to the pillar walls and to the perimeter walls, chemical anchoring based on threaded bars injected with pure Bossong BCR-400 EPOX epoxy resin was used.
Considering the importance of the loads involved and the influence of the type and condition of the sub-layer, in this case we were dealing with full brick walls, on the adherence developing between the epoxy resin and the base material, we had to carry out some on site pull-out tests to check on the effective base material resources.
The on site extraction test stages:
Drilling, Cleaning of the Hole, BCR-400 EPOX resin extrusion, cure time necessary, pull-out test.
Other problems linked to applying resin anchorage which characterize sites for the recovery of historical buildings and objects: the need to block scaffolding to the walls often requires the use of chemical anchoring, as damaged walls cannot guarantee the best conditions for the installing of mechanical anchoring.
The wooden structures themselves, often garrets and roofing, can need strengthening implying the insertion of metal elements combined with epoxy resin.
In all these applications, the weak anchoring element is the substrate, of wall or wood which, unlike concrete, is highly variable; that is why the on site tests are really important for applications on materials whose resistance characteristics change according to type and state of conservation, as experimental reference tests are always carried out in laboratory on materials with standard characteristics and in excellent conditions.